Remember, you fly an airplane with your head, not your hands and feet
AnonymousThis is a particularly complex time for civil aviation, and the current health emergency is adding a new dimension to air travel. Full-body ‘sanitisation’ technologies are being tested and are likely to become permanent practice alongside security measures. Despite the exceptional nature of the current situation, we must not forget the future technological challenges that are changing the world of aerospace systems.
Technological evolution in aircraft such as planes, flying robot-taxis and drones, is driven by the macro-trends of multimodal transport, the goal of reducing environmental impact, and the revolution of the travel experience. Multimodal transport aims to integrate systems to improve mobility, in terms of overall transfer times and the optimisation of travel routes. Reducing environmental impact is driving the use of increasingly ‘green’ propulsion systems. Finally, there is talk of space tourism as a new business opportunity for extra-luxury trips around the Earth’s orbit, for a breathtaking experience.
All this development would not be possible without the high safety standards that characterise the aerospace system, such as DO331 and DO178C. Virtual and digital modelling and simulation will increasingly be the operational tools used to achieve innovation in this sector, and will have important effects in terms of reducing development time and costs. Teoresi has extensive experience in modelling and prototyping complex systems, combined with excellence in device testing.
Research is focused on reducing the ecological impact of flying, with an important focus on hybrid-electric propulsion. Some countries aim to reduce pollution from civil aircraft by 90%, especially on some shorter routes. This ambitious target must also take the role of electric power in aerospace into account. We are now seeing the launch of hi-tech companies that claim to design and develop electric aircraft. Air taxis will soon become a reality on shorter routes, as will drone delivery. This requires new design, batteries and infrastructure.
Artificial intelligence will play a dual role: on the one hand, it will lead to an increase in predictive maintenance, which is already happening in the rail and automotive sectors. On the other, it will enable ground systems to route air traffic intelligently, from large aircraft to drones.
Autonomous driving technologies for this sector are in full development. Autonomous planes are already feasible today, planes that can optimise flights in real time on a set trajectory. In the future, these planes will be able to take traffic, weather and turbulence into account themselves, using sophisticated AI applications. Reducing flight waiting times is another major goal for the future.. We are talking about reducing the total flight time, including flying, parking and inspections by at least 50%. Configurable aircraft which rearrange interior spaces in real time, based on the number of passengers, are also being studied.
Simulation is the key to success regardless of the type of innovation being undertaken, be it a more aerodynamic fuselage, autopilot software or an electric drone. The development of a flight system currently involves years of design and testing, costing billions of euros. Simulation techniques combined with rapid prototyping make a strong contribution to reducing costs. There are different methods of aerospace simulation: Model Based System Engineering (MBSE) for system requirements, Model Based Design (MBD) for software design, CAD/CFD for 3D simulations of aerodynamic flows and structure.
The development of software for aerospace systems is particularly critical and costly.
60-70% of the cost of an aircraft, whether civil or military, or of a simple device is invested in the verification and validation process of on-board systems and equipment. The design process must be rigorous and in accordance with standards such as DO-178C.
Simulation combined with MBSE/MBD techniques cuts design, development and testing times and also integrates seamlessly with the various certification standards. High performance HIL prototyping techniques make it possible to test the system.
Model and software testing techniques are well suited to automation and compared to the system requirements, they further reduce the costs of the verification and validation phase.
Teoresi has years of experience in modelling and software production in the aerospace sector.
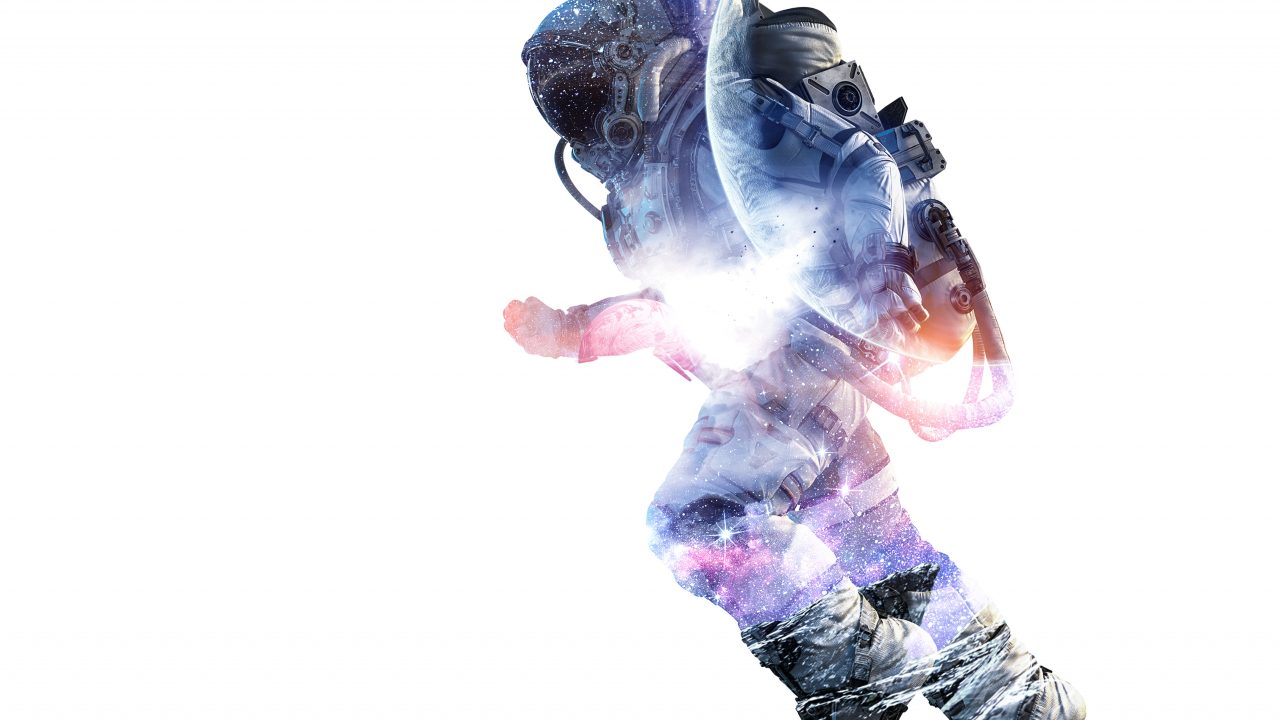
Teoresi works according to the DO178C standard for different types of aerospace equipment, drafting functional requirements, managing them and specifying the corresponding system and component tests.
Our methodology includes a team dedicated to RAMS (Reliability, Availability, Maintainability, and Safety) analysis and teams with experience in modelling and code generation in accordance with MBSE systems engineering or Model Based Design. The Teoresi staff also take care of ILS (integrated logistic support) in some projects.
In systems engineering we use state of the art technologies for requirements management, for both systems and components. In Model Based Design we apply the full V-cycle with continuous integration and different methodologies, including Agile. We have worked on tactical planning and mission control systems, FCS (Flight Control Systems) and innovation systems for electric engines.
In aerospace interfaces for cockpits, we use our 20 years’ of HMI development experience as well as the automatic interface test systems that we develop and maintain.
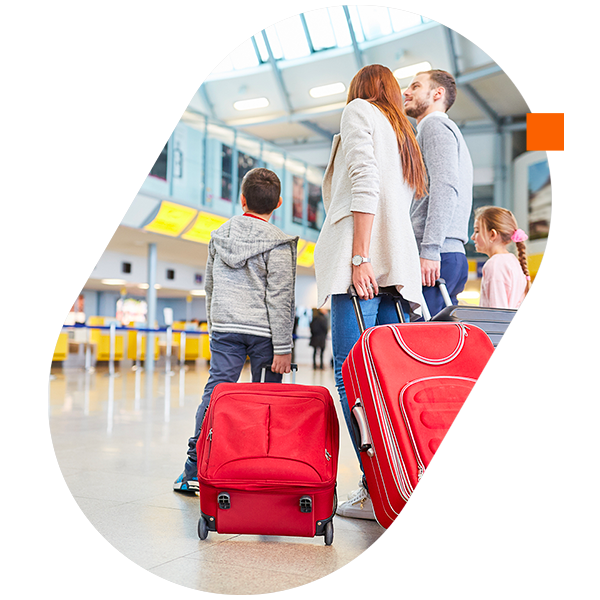
The new advances in aircraft, such as the widespread use of electrical systems and autonomous piloting algorithms, have also benefited from Teoresi’s experience in prototyping difficult systems, such as electromechanical systems or energy storage systems. Our automotive experience enables us to address similar problems in the aerospace industry.
